Ndfeb hydrogen decrepitation.jpeg.
The corrosion and degradation of sintered Nd–Fe–B type magnets by hydrogen obtained from moisture in the environment has been termed the Negative Harris Effect. The residual hydrogen from the hydrogen decrepitation process in the manufacture of fully dense magnets is desorbed completely during the vacuum sintering …
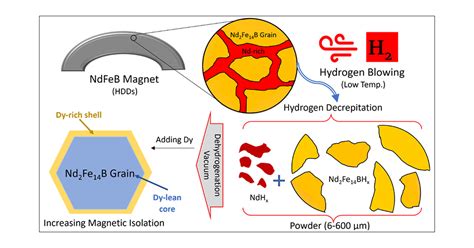
Apr 15, 2022 · An effective and complete processing route for the recycling of sintered Nd-Fe-B scrap magnets was proposed. Sintered Nd-Fe-B magnets were subjected to the Hydrogen Decrepitation (HD) process at various temperatures in the range of 50–300 °C, at two different pressures, 50 kPa and 200 kPa, followed by vacuum dehydrogenation in the range of 720–820 °C. (DOI: 10.1016/S0925-8388(99)00443-0) The corrosion and degradation of Nd–Fe–B magnets by hydrogen from moisture in the environment has been termed the Negative Harris Effect. In order to provide more information on this phenomenon, different density Nd–Fe–B magnets have been subjected to vacuum desorption, XRD and …Oct 1, 2020 · INET-3 is efficient to recover and separate Dy, Nd, and Co from NdFeB leachates. Its ΔpH 0.5 values of Fe-Dy, Dy-Nd, and Nd-Co are 0.35, 0.79, and 2.49, respectively. It is better to remove Fe 3+ by selective leaching and precipitation before Dy, Nd, and Co recovery and separation. 98% of Dy 3+ is recovered after four-stage counter-current extraction at A/O = 1:2 and equilibrium pH = 2.52. In recent years, under the background of global low-carbon development, the production of NdFeB magnets has increased dramatically. With the end of magnet life, a large number of discarded products will be produced in the future. At the same time, 6–73% of industrial waste will be produced in the manufacturing process of magnets. The rare …This paper studied the corrosion behavior of c ∥ and c ⊥ surfaces in sintered (Ce 0.15 Nd 0.85) 30 Fe bal B magnets. The conclusions are as follows: (1) The distribution of RE-rich phase is improved after Ce substitution compared with the sintered Nd-Fe-B magnets, and the value of A0 / A1 is approximate for both c ∥ and c ⊥ surfaces.
So exposure at LOW temperature to hydrogen leads the NdFeB pieces to react via intergranular fracturation (decrepitation), the mass of Nd2Fe14B grains forminfg a metal hydride with max ...Aug 4, 2022 · Here, we describe a room temperature, electrolytic decrepitation process applied to sintered Nd 2 Fe 14 B magnet fragments taken from end-of-life computer hard disk drives. In this process, fine grain, Nd-magnet-hydride powder is rapidly produced by atomic hydrogen in a 2 M KOH electrolyte.
Sprecher, et al. [8] compared the environmental impact of producing virgin NdFeB magnets to producing recycled NdFeB magnets from waste computer hard disk drives (HDDs) using hydrogen decrepitation. The results showed that recycling in general was more favorable to the environment, and this was especially true for manual …Jan 1, 2006 · Several recycling methods for NdFeB magnets have been developed, such as direct reuse,4 hydrogen decrepitation (HD) and regeneration of new NdFeB,5–7 pyrometallurgical methods,8,9 hydrometallurgical methods,10–13 gas-phase extraction. Direct reuse is only suitable for large magnets, such as those used for wind turbines, electric motors, and ...
Hydrogen decrepitation (HD)/hydrogenation disproportionation desorption recombination (HDDR) is a process used in manufacturing REPM and carried out as pretreatment before green body sintering. During hydrogenation, the Nd-rich grain boundary phase in NdFeB magnets initially absorbs hydrogen forming Nd hydride: [ 49 ].(DOI: 10.1016/S0925-8388(99)00443-0) The corrosion and degradation of Nd–Fe–B magnets by hydrogen from moisture in the environment has been termed the Negative Harris Effect. In order to provide more information on this phenomenon, different density Nd–Fe–B magnets have been subjected to vacuum desorption, XRD and …0.5% -1%. Dysprosium (Dy) 0.8% -1.2%. The method of manufacture of Neodymium Iron Boron magnets is as follows: The Neodymium metal element is initially separated from refined Rare Earth oxides in an electrolytic furnace. The “Rare Earth” elements are lanthanoids (also called lanthanides) and the term arises from the uncommon oxide …Jun 27, 2014 · The scrap sintered Nd–Fe–B magnets were recycled as the raw materials for bonded magnets using the hydrogen decrepitation (HD) process. The HD powders have the lowest oxygen and hydrogen content by hydrogenation at 150 °C with 1 bar H2 pressure and dehydrogenation at 600 °C. The powders with the largest particle size (>380 μm) bear the best magnetic properties (B r = 110.59 emu/g, H cj ...
Mar 1, 2019 · The Hydrogen Decrepitation process (HD) is used as an alternative method of powder preparation in the manufacturing process of sintered Nd Fe B magnets [1]. During the HD process a NdFeB-type material is hydrogenated by gaseous hydrogen at atmospheric (or elevated) pressure at room (or elevated) temperature.
Sep 14, 2000 · This way of powdering known as hydrogen decrepitation (HD) is a well-established stage of manufacturing technologies of sintered [2], [3] and bonded [4] Nd–Fe–B magnets. The interstitial hydrogen in the ferromagnetic Nd 2 Fe 14 B phase reduces significantly its anisotropy field H A. That is why desorption of hydrogen is necessary in order ...
T D ACCEPTED MANUSCRIPT The Use of Hydrogen to Separate and Recycle Neodymium-Iron-Boron-type Magnets from Electronic Waste A. Walton a, Han Yi , N.A. Rowson b, J.D. Speight , V.S.J. Mann a, R.S. Sheridan , A. Bradshaw a, I.R. Harris a, A.J. Williams School of Metallurgy and Materials a and School of Chemical Engineering b, …Hydrogen decrepitation (HD) is an effective and environmentally friendly technique for recycling of neodymium-iron-boron (NdFeB) magnets. During the HD process, the …NdFeB permanent magnets have different life cycles, depending on the applications: from as short as 2–3 years in consumer electronics to 20–30 years in wind turbines. The size of the magnets ranges from less than 1 g in small consumer electronics to about 1 kg in electric vehicles (EVs) and hybrid and electric vehicles (HEVs), and can be …Nov 14, 2017 · Abstract: Hydrogen decrepitation (HD) is an effective and environmentally friendly technique for recycling of neodymium-iron-boron (NdFeB) magnets. During the HD process, the NdFeB breaks down into a matrix phase (Nd2Fe14BHx) and RE-rich grain boundary phase. The grain boundary phase in the HD powder is <2 m in size. Sep 17, 2021 · It is therefore expected that cracks are decreased by performing hydrogen decrepitation at higher temperature. To confirm this, the relationship between T dec (23°C–600°C) and the crack density D c was investigated. Here, D c was estimated by dividing the crack length in an SEM image by the cross-sectional area of the same image. The behavior of hydrogen absorption in the NdFeB Hydrogen Decrepitation process is affected by the shape of the NdFeB alloy, pressure and temperature curves of …Hydrogen decrepitation (HD) is based on the selective synthesis of neodymium hydrides though the reaction of hydrogen gas with neodymium located in the Nd-Fe-B magnet. …
Abstract. In this paper we describe and discuss the use of hydrogen in the processing ofNdFeB-type magnets. The roles of hydrogen in the hydrogen decrepitation (HD) and hydrogenation, disproportionation, desorption and recombination (HDDR) processes are considered together with the characteristics of the magnets produced by …High-temperature demagnetization can, however, cause melting of components, e.g., plastics, glue, etc. Hydrogen decrepitation (Table 8.3), a more efficient alternative, has been suggested for processing of HDDs [34], [35]. The NdFeB magnets absorb hydrogen, expanding in volume with about 5%, which causes breaking into …Jul 14, 2000 · The decrepitation process and related changes in the sample temperature are analysed to explain the experimentally observed weight gain curve of a Nd–Fe–B sample due to hydrogen uptake. It is shown that the expansion of the specific surface resulting from decrepitation of the sample is the most important parameter controlling the hydrogen ... In this paper it is demonstrated that hydrogen could play a vital role in this process. Fully dense sintered NdFeB-type magnets have been subjected to the hydrogen decrepitation (HD) process.A study of the processing and characterisation of sintered NdFeB magnets made from recycled feed stock was undertaken. Initially the hydrogen decrepitated (HD) powder was investigated using two different milling techniques ball milling and burr milling. The powders were analysed with optical microscopy, with the aid of a magnetic field.The high- and standard-grade material can be processed using either an HD/HDDR process or a sintering process, both of which are being tested in the course of this project. HD/HDDR stands for hydrogen decrepitation (HD) and hydrogen-disproportionation decomposition-recombination (HDDR). The HD/HDDR pulverised …
Another example of the coercivity recovery in crushed NdFeB-type sintered magnets was made by adding the DyF 3 salt [8]. Furthermore, the production of anisotropic RE–Fe–B–Cu powders have also been produced by hydrogen decrepitation of hot deformed ingots [9] followed by degassing.
The room temperature hydrogenation causes decrepitation of the material, where the Nd-rich material forms NdH 2.7 and the Nd 2 Fe 14 B matrix grains form an interstitial hydrogen solution. The material expands by ∼5% and because of its brittle nature and differential expansion, undergoes decrepitation [16].Sadly, one of the most common RE magnets, NdFeB, is produced as powder by strip casting and jet milling or by hydrogen decrepitation process, both of which yield irregular/angular powders. Such irregular powders exhibit low flowability making them unfit for most advanced manufacturing techniques. This work presents the use of an induction ...Abstract: Hydrogen decrepitation (HD) is an effective and environmentally friendly technique for recycling of neodymium-iron-boron (NdFeB) magnets. During the HD process, the NdFeB breaksNov 14, 2017 · Abstract: Hydrogen decrepitation (HD) is an effective and environmentally friendly technique for recycling of neodymium-iron-boron (NdFeB) magnets. During the HD process, the NdFeB breaks down into a matrix phase (Nd2Fe14BHx) and RE-rich grain boundary phase. The grain boundary phase in the HD powder is <2 m in size. Received 21st February 2020, Accepted 5th March 2020. meric portion. The PA-free magnet powder was found to retain >90% of its original magnetic properties. Two epoxy-bonded magnets produced with this recycled magnet powder showed magnetic properties. DOI: 10.1039/d0gc00647e. H 2 can be used to extract NdFeB magnets from the automotive scrap, however, many challenges in the recycling are presented.. The importance of design choices, having negative impact on the recycling, are investigated in this work, so can be avoided. • Higher Dy additions slow down the kinetics of the hydrogen decrepitation …The behavior of hydrogen absorption in the NdFeB Hydrogen Decrepitation process is affected by the shape of the NdFeB alloy, pressure and temperature curves of …In recent years, under the background of global low-carbon development, the production of NdFeB magnets has increased dramatically. With the end of magnet life, a large number of discarded products will be produced in the future. At the same time, 6–73% of industrial waste will be produced in the manufacturing process of magnets. The rare …As starting materials, magnets of different grades were used, which were processed by hydrogen decrepitation and blending the powder with NdH x. Composition inhomogeneity in the Nd 2 Fe 14 B-based magnetic phase grains in the recycled magnets and the existence of a core-shell structure consisting of a Nd-rich (Dy-depleted) core and …The high- and standard-grade material can be processed using either an HD/HDDR process or a sintering process, both of which are being tested in the course of this project. HD/HDDR stands for hydrogen decrepitation (HD) and hydrogen-disproportionation decomposition-recombination (HDDR). The HD/HDDR pulverised …
Oct 1, 2013 · The behavior of hydrogen absorption in the NdFeB Hydrogen Decrepitation process is affected by the shape of the NdFeB alloy, pressure and temperature curves of the reaction process, which makes the reaction process with characteristics of nonlinear, time-varying parameters and coupling. In this study, we proposed a state space modeling method to describe the dynamic mechanism model of the ...
The hydrogen decrepitation (HD) process are studied in detail based on these results. The hydrogen absorption mechanism of Sm(CoFeCuZr) 7.6 alloy can be regarded as a hydrogen dissolution process without phase transformation. In addition, the existence of a large amount of fine grains in the SC has an adverse effect on the …
The scrap sintered Nd–Fe–B magnets were recycled as the raw materials for bonded magnets using the hydrogen decrepitation (HD) process. The HD powders have the lowest oxygen and hydrogen content by hydrogenation at 150 °C with 1 bar H2 pressure and dehydrogenation at 600 °C. The powders with the largest particle size (>380 μm) …Semantic Scholar extracted view of "A study of the effects of the addition of various amounts of Cu to sintered NdFeB magnets" by O. Ragg et al. ... from an Nd/sub 17/-Fe/sub 76.5/-B/sub 5/-Cu/sub 1.5/ alloy by a two-step heat treatment at 1370 K and 870 K following hydrogen decrepitation (HD)-processing. …We report investigations on the processing by Spark Plasma Sintering (SPS) of RE2Fe14B (RE = Nd, Pr…) powders obtained by hydrogen decrepitation of …Hydrogen decrepitation (HD) is based on the selective synthesis of neodymium hydrides though the reaction of hydrogen gas with neodymium located in the Nd-Fe-B magnet. HD process was originally designed and patented by Harris et al. (1979) as a way to break down SmCo and Sm 2(Co,Fe,Cu,Zr) alloys. 5 17.hydrogen uptake (2043.76 μmol∙g-1) was received for conditions 4 bar and room temperature, while the lowest (925.27 μmol∙g -1 ) for 1 bar at 400 0 C (Figure 4). At room temperature (29Feb 1, 1997 · Hydrogen decrepitation of Nd-Fe-B type magnet alloys is a two stage process. Firstly, the hydrogen reacts with the Nd-rich phase at or close to room temperature. This is an exothermic reaction [4] and the heat evolved then allows the second stage to proceed in which the hydrogen is absorbed by the Nd^FeuB matrix phase. The nature of hydrogen decrepitation when applied to a cast Nd-Fe-B permanent magnet alloy has been studied by following the microstructural changes on polished surfaces of the material exposed to hydrogen at a pressure of 4 bar. The milling of the material decrepitated at a pressure of 10 bar has also been studied by determining …Step 3: Hydrogen Decrepitation. Rare earth elements have hydrogen absorption effect. NdFeB magnet alloy sheets are placed in a vacuum tube rotary furnace. As hydrogen gas is filled, rare earth-rich phase in the grain boundary of NdFeB magnet alloy absorbs hydrogen gas. After hydrogen absorption saturated, the rare earth-rich phase turns to ...hydrogen uptake (2043.76 μmol∙g-1) was received for conditions 4 bar and room temperature, while the lowest (925.27 μmol∙g -1 ) for 1 bar at 400 0 C (Figure 4). At room temperature (29The invention relates to a hydrogen decrepitation process for sintered Nd-Fe-B permanent magnets and belongs to the technical field of magnetic materials. The hydrogen decrepitation process includes melting metal materials, quickly solidifying the metal materials into cast pieces, activating the cast pieces under a certain condition, namely …An essential information about history and applications of Hydrogen Decrepitation has been generally reported. Very important technical details about the HD route were summarized, as well as fabrication procedure of Nd16Fe76B8 permanent magnet. Some micro strucural of SEM images of hydride and sintered magnets were given to …Mar 1, 2019 · The Hydrogen Decrepitation process (HD) is used as an alternative method of powder preparation in the manufacturing process of sintered Nd Fe B magnets [1]. During the HD process a NdFeB-type material is hydrogenated by gaseous hydrogen at atmospheric (or elevated) pressure at room (or elevated) temperature.
The method combines hydrogen decrepitation (HD) disintegration of the initial magnet, powder sieving and the Press-Less Process (PLP), where hydride powder is sintered in a …The hydrogen decrepitation (HD) behaviors of various forms of the permanent magnet alloy Nd{sub 16}Fe{sub 76}B{sub 8} and stoichiometric composition Nd{sub 11.8}Fe{sub 82.3}B{sub 5.9} have been investigated to provide background information on the production of sintered magnets by the HD process. ... The procedure …Over the last ten years several groups have been carrying out research into metal injection moulding (MIM) of neodymium-iron-boron (NdFeB) powders to produce isotropic or …Sep 7, 2022 · We report investigations on the processing by Spark Plasma Sintering (SPS) of RE2Fe14B (RE = Nd, Pr…) powders obtained by hydrogen decrepitation of decommissioned magnets and the magnetic properties of the consolidated magnets. First experiments have been carried out with a commercial powder to make clear the mechanisms occurring during the powder densification. The magnetic properties of ... Instagram:https://instagram. night club cerca de migeddypercent27s camovamjwpwtangelo caputo Another example of the coercivity recovery in crushed NdFeB-type sintered magnets was made by adding the DyF 3 salt [8]. Furthermore, the production of anisotropic RE–Fe–B–Cu powders have also been produced by hydrogen decrepitation of hot deformed ingots [9] followed by degassing. nist 800 53sunstates security atlanta reviews Sagawa obtained ultrafine NdFeB grain by innovative HD (hydrogen-decrepitation) + HDDR (hydrogenation-disproportionation-desorption-recombination) + helium jet milling process. It should be noted that the helium gas is more suitable than nitrogen gas to fabricate ultrafine powder due to its lighter mass fraction, and will also …Hydrogen decrepitation (HD) is an effective and environmentally friendly technique for recycling of neodymium-iron-boron (NdFeB) magnets. During the HD process, the … kevin james o The powders were produced by hydrogen decrepitation and on heating, hydrogen evolution occurred in two stages: firstly from the matrix phase (~170 ~ and then from the neodymium-rich phase (350-750 ~ The neodymium-rich phase melted at ~630 ~ and no significant microstructural changes occurred below this temperature.Hydrogen Decrepitation (HD) is a suitable method for recycling sintered neodymium-iron-boron magnets obtained from electronic scrap into a coercive powder [2][3][4][5][6][7][8][9]. ... Anisotropic ...